An Extensive List for Effective Welding Inspection Practices
In the realm of welding, the stability of structures is vital, demanding a strenuous technique to evaluation practices. An extensive list works as a crucial device in making sure adherence to industry standards, incorporating essential pre-welding, in-process, and post-welding examinations. By systematically dealing with product confirmation, weld top quality, and thorough documents, organizations can significantly boost safety and security and performance. What details aspects should be focused on in each stage to accomplish optimum outcomes? Checking out these critical elements can generate insights that exceptionally effect welding procedures.
Understanding Welding Requirements
Welding requirements play an important function in guaranteeing the quality and security of welded components and structures. These criteria establish the requirements for products, procedures, testing, and inspection, therefore offering a framework for consistent quality guarantee in welding procedures. Various companies, consisting of the American Welding Culture (AWS), the International Company for Standardization (ISO), and the American Society of Mechanical Engineers (ASME), have established extensive requirements that regulate various facets of welding.
Comprehending welding requirements is important for specialists in the field, as adherence to these standards lessens the threat of defects and failures in welded joints. These requirements cover details needs for weld top quality, including acceptable resistances, the sort of welding methods to be utilized, and the credentials needed for inspectors and welders.
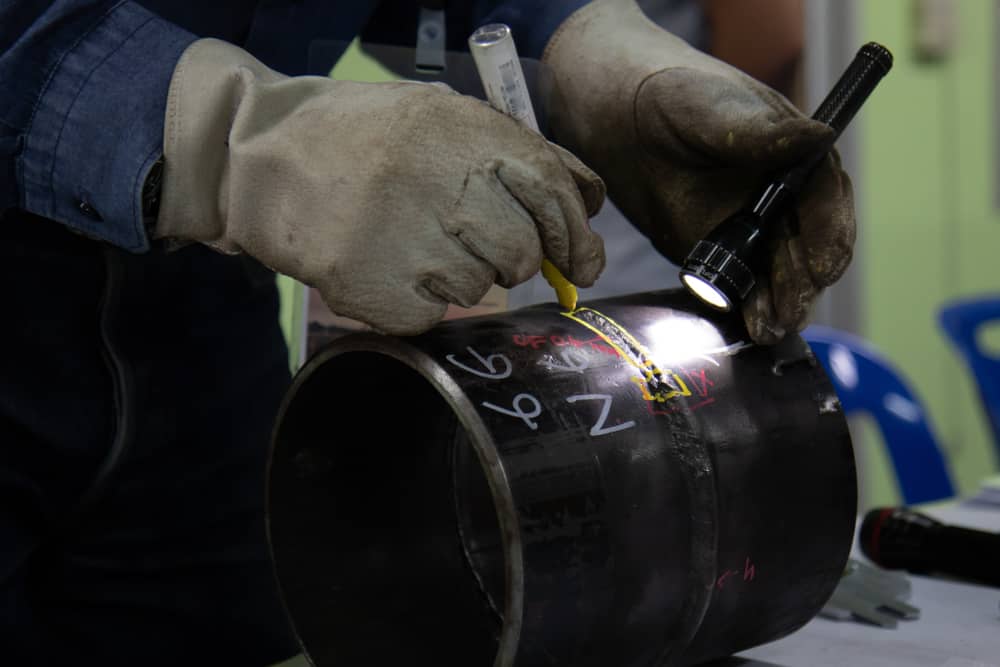
Pre-Welding Evaluation Actions
Prior to any kind of welding procedure commences, an extensive pre-welding inspection is important to recognize prospective concerns that might endanger the quality of the weld. This preliminary step serves as an essential structure for making certain compliance with suitable welding codes and standards.
The very first action in the pre-welding assessment is to verify the products being utilized. Next off, it is vital to inspect the fit-up of the elements to make sure appropriate placement and joint arrangement.
Furthermore, evaluating the tidiness of the surfaces is essential; impurities such as corrosion, paint, or oil can adversely impact the top quality of the weld. Following this, a detailed analysis of the welding equipment should be conducted, guaranteeing that it is calibrated and in excellent working problem.
Lastly, reviewing the qualifications of the welding workers is crucial. Welders should possess the needed accreditations and experience to execute the certain welds needed for the project. By adhering to these pre-welding assessment actions, the probability of defects and failings in the final weld can be considerably minimized.
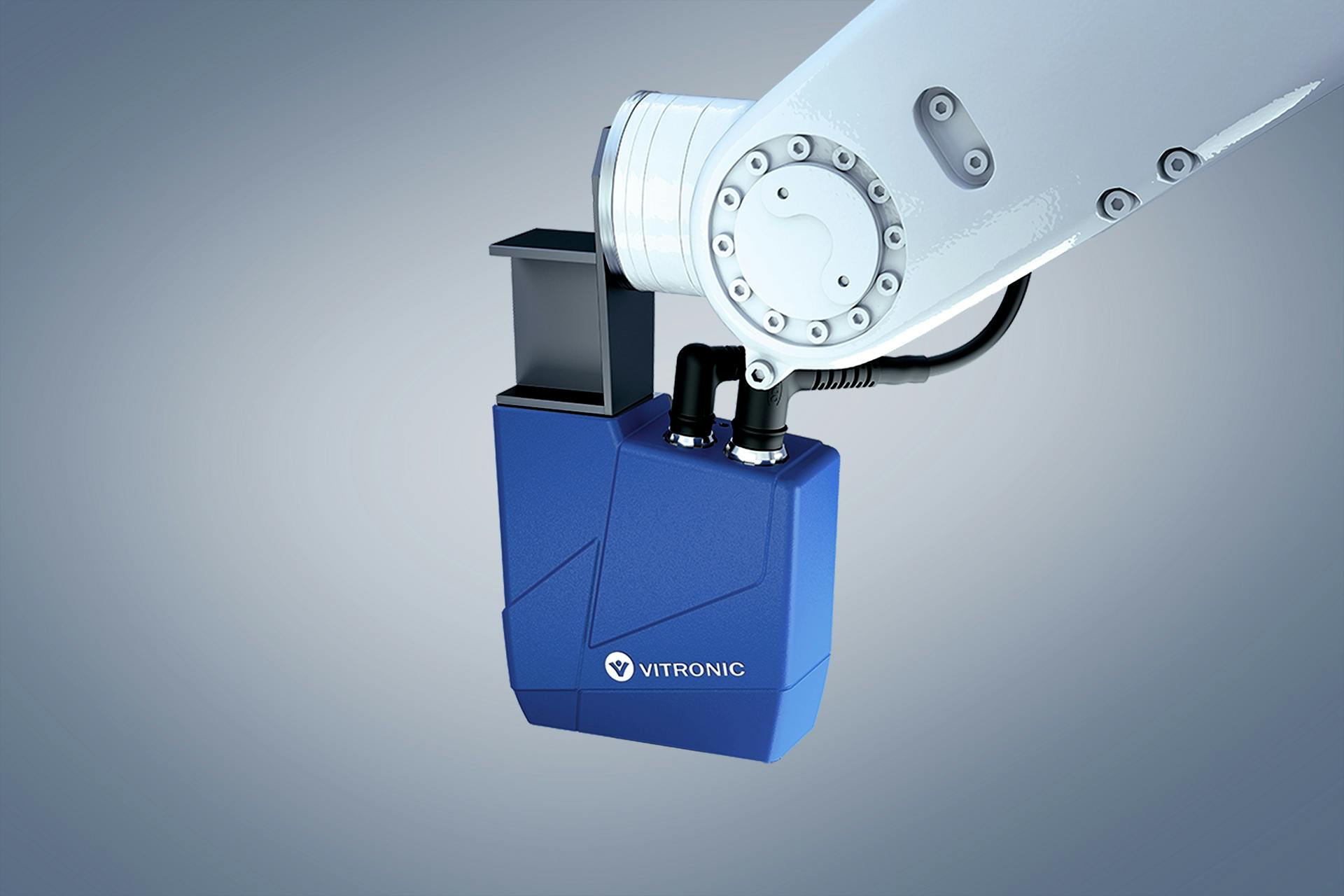
In-Process Inspection Methods
In-process inspection methods play a crucial function in making certain the integrity and high quality of welds as they are being performed. These techniques enable inspectors to recognize issues or discrepancies from specifications in genuine time, consequently preventing costly repair work and making sure adherence to design needs.
One key method entails visual examination, where examiners assess the weld bead for harmony, infiltration, and appropriate profile. This can be matched by the use of gauges to determine weld page dimensions, making certain conformity with fixed tolerances. Additionally, the execution of non-destructive testing (NDT) approaches, such as ultrasonic testing or magnetic fragment screening, during the welding process can disclose subsurface problems that may not be noticeable on the surface.
Another vital aspect is monitoring welding parameters, consisting of voltage, amperage, and travel speed. Uniformity in these specifications is crucial for achieving ideal weld high quality. Recording these specifications during the welding procedure provides a deducible document for future recommendation.
Training employees in proper examination methods and using appropriate devices enhances the effectiveness of in-process inspections. By integrating these methods, companies can accomplish higher quality welds, lower rework, and inevitably ensure the safety and integrity of welded structures.
Post-Welding Top Quality Checks
Following the conclusion of welding operations, post-welding top quality checks are crucial to verify that the welds fulfill all defined criteria and requirements. These checks are vital for ensuring the stability and sturdiness of the bonded joints. The examination process generally starts with a visual evaluation, assessing for surface area issues such as cracks, porosity, or incomplete blend.
Subsequently, non-destructive screening (NDT) methods, such as ultrasonic testing, radiographic screening, or magnetic fragment testing, may be utilized to find interior defects that are not noticeable to the naked eye. Each technique has its unique advantages and is picked based on the weld's place, product type, and the go to the website nature of the application.
Additionally, confirming dimensional precision is an important facet of post-welding high quality checks. This entails gauging the weld's alignment, dimension, and profile to make sure conformity with engineering requirements. Analyzing the mechanical homes of the weld, consisting of tensile toughness and ductility, can give additional guarantee of performance under operational conditions. On the whole, detailed post-welding evaluations are crucial for maintaining performance, safety and security, and adherence to governing and sector requirements.
Documents and Coverage
Just how can effective paperwork and reporting boost the welding assessment procedure? Exact documentation and comprehensive reporting are crucial components that ensure the honesty and quality of welding operations. Welding Inspection Milwaukee. They function as an official record of evaluation findings, facilitating liability and traceability in conformity with industry requirements

A well-structured reporting system enables examiners to clearly connect any kind of areas, disparities, or non-conformances calling for enhancement. This transparency cultivates an environment of continuous enhancement, as stakeholders can readily analyze previous efficiency and apply corrective actions.
Additionally, efficient documentation consists of thorough records such as welding treatment specifications (WPS), welder credentials, and inspection lists. These components supply a framework for evaluating weld quality and adherence to established guidelines. In case of conflicts or top quality issues, thorough documents works as a trusted reference, reducing ambiguity and safeguarding all parties involved.
Last but not least, maintaining organized documents aids in training and licensing employees, ensuring that sector ideal methods are supported. Eventually, meticulous documentation and reporting not just enhance the welding evaluation process but additionally add to the overall security and reliability of bonded frameworks.

Final Thought
In verdict, visit this website a comprehensive list for effective welding examination techniques is important for making sure quality and safety in welded structures. Adherence to established welding standards, meticulous pre-welding assessments, rigorous in-process analyses, and extensive post-welding high quality checks collectively contribute to the honesty of bonded joints.
Welding criteria play a vital duty in ensuring the top quality and safety and security of welded parts and structures. Various companies, consisting of the American Welding Culture (AWS), the International Organization for Standardization (ISO), and the American Society of Mechanical Designers (ASME), have actually developed comprehensive standards that control various facets of welding.
Complying with the completion of welding operations, post-welding top quality checks are crucial to confirm that the welds meet all specified requirements and standards - Welding Inspection Milwaukee.In conclusion, a detailed checklist for reliable welding evaluation methods is important for making certain quality and safety and security in welded structures. Adherence to developed welding standards, precise pre-welding evaluations, rigorous in-process analyses, and thorough post-welding quality checks collectively contribute to the stability of bonded joints